TEMA 5
MECANIZADO BÁSICO
Bienvenido una vez más, hoy hablaremos de los distintos conocimientos y herramientas que debemos de adquirir de cara a realizar procesos de mecanizado.
Vamos a empezar por el Trazado y sus herramientas:
El trazado es un paso previo antes de realizar el mecanizado de una pieza, y consiste en delimitar sobre la pieza lo que queremos realizar en ella, un ejemplo, marcar los centros para taladrar, líneas de corte etc. En gran parte un buen trazado influirá en el resultado final de la pieza, por eso hay que realizarlo lo mejor posible.
Pasando ya con las herramientas, debemos saber que se pueden agrupar en dos grupos
- Útiles de Trazado
- Instrumentos auxiliares para el trazado
Útiles de Trazado
Son los encargados de señalar las marcas o líneas de referencia sobre la pieza.
Los más importantes son:
- Punta de trazar: Se utiliza para trazar líneas rectas o curvas, mediante el apoyo en la correspondiente regla o guía. Es una varilla de acero fundido, cuyos extremos están templados y afilados a unos 10º.
- Gramil: Se utiliza para trazar líneas paralelas a diferente altura con respecto al mármol sobre el que se apoya y desplaza. En ocasiones también se utiliza como instrumento de verificación para comprobar el paralelismo y el centrado de las piezas.
- Granete: Es una herramienta de acero templado, similar a un trazador, pero con una punta redondeada. Sirve para marcar el centro donde se tiene que taladrar y sirve de guía a la broca, para conseguir esto debemos golpear levemente la cabeza del granete con un martillo.
-Compás: Al igual que un compás normal, es utilizado para trazar arcos de circunferencia o circunferencias completas, transportar distancias, etc. Pero antes de nada debemos granetear el centro de giro, para evitar que la punta pueda resbalar.
Instrumentos auxiliares para el trazado
Los vamos a dividir en tres grupos:
- Soportes
- Guías
- Barnices y cubrientes
-Soportes: Estos elementos se emplean como apoyos de las piezas para facilitar la tarea de trazado. Los más utilizados son:
Mármol
Es una mesa fabricada muy resistente de hierro fundido, su cara superior está totalmente pulida y sirve para hacer de apoyo o guía a los diferentes útiles de trazado.
Escuadras y cubos de trazado
Como su propio nombre indica son piezas de de fundición gris a las cuales se les da la forma de escuadra y de cubo, que contiene unos orificios para la mejor sujección de las piezas a mecanizar.
 |
Escuadra de Trazado |
 |
Cubo de trazado |
Calzos
Los calzos son elementos prismáticos fabricados con fundición gris, donde sus caras son paralelas entre sí y contienen superficies inclinadas formando 90º, donde apoyaremos las piezas cilíndricas.
-Guías: Sirven, como su propio nombre indica, para hacer de guía a los útiles de trazado, colocándose sobre la pieza a marcar. Los más utilizados son:
- Reglas: Son idénticas a las de dibujo técnico pero de materiales más resistentes para su uso diario en el taller,
- Escuadras: Son de acero de carbono templado y se utilizan para el trazado de líneas paralelas, perpendiculares o inclinadas.
 |
Regla |
 |
Escuadra |
-Barnices y cubrientes: Son unas pastas colorantes diluidas que se utilizan para pintar sobre el trazo para apreciarlo mejor, ya que la mayor parte de la superficie de las piezas va a ser bastante brillante.
De esta forma se facilita la visibilidad del trazado.Estos productos secan rápidamente sin "desconcharse", son fáciles de eliminar, y producen una película de tonalidad mate que permite un contraste óptimo. Los más usados son:
- Blanco de España, una mezcla de agua con cola disuelta.
- Azul de Prusia, una mezcla que lleva alcohol y goma laca.
- Mezcla de sulfato de cobre y agua.
- Disoluciones (ya preparadas) para colorear.
 |
Mezcla Blanco de España |
 |
Mezcla Azul Prusia |
Sistemas y herramientas de control dimensional
Este tipo de herramientas son instrumentos de medición muy precisa, no se puede comparar con reglas o similares, y dependiendo de la situación elegiremos unos u otros, los más frecuentes son los siguientes:
-Calibre: Es un instrumento para medir las dimensiones de objetos muy pequeños o que seria imposible precisar una medida exacta mediante los métodos tradicionales.
En la escala de las pulgadas tiene divisiones equivalentes a 1/16 de pulgada y, en su nonio, de 1/128 pulgadas.
Consta de una regla con una escuadra en un extremo, sobre la cual se desliza otra destinada a indicar la medida en una escala. Permite apreciar longitudes de 1/10, 1/20 y 1/50 de milímetro utilizando el nonio.
Mediante piezas especiales en la parte superior y en su extremo, permite medir dimensiones internas y profundidades.
Posee dos escalas: la inferior milimétrica y la superior en pulgadas.
-Micrómetro: Es un instrumento de medición cuyo funcionamiento está basado en el tornillo micrométrico y que sirve para medir las dimensiones de un objeto con alta precisión, del orden de centésimas de milímetro (0,01 mm) y de milésimas de milimetro (0,001 mm).
Para ello cuenta con dos puntas que se aproximan entre sí mediante un tornillo de rosca fina, el cual tiene grabado en su contorno una escala.
La escala puede incluir un nonio, la máxima longitud de medida del micrómetro de exteriores es de 25 mm, por lo que es necesario disponer de un micrómetro para cada campo de medidas que se quieran tomar (0-25 mm), (25-50 mm), (50-75 mm), etc.
Frecuentemente el micrómetro también incluye una manera de limitar la torsión máxima del tornillo, dado que la rosca muy fina hace difícil notar fuerzas capaces de causar deterioro de la precisión del instrumento.
-Reloj comparador: Un reloj comparadores un aparato que transforma el movimiento rectilíneo de las puntas de contacto, en movimiento circular de las aguas del reloj.
Por sus propios medios no da lectura directa, pero es útil para comparar las diferencias que existen en la cota de varias piezas que se quieran verifica. La capacidad para detectar la diferencia de medidas es posible gracias a un mecanismo de engranajes y palancas, que van metidos dentro de una caja metálica circular. Dentro de esta caja se desliza un eje, que tiene una punta esférica que hace contacto con la superficie. Este eje, al desplazarse, mueve la aguja del reloj, y hace posible la lectura directa y fácil de las diferencias de medida.
La precisión de un reloj comparador puede ser de centésimas de milímetros o incluso de milésimas de milímetros (micras), según la escala a la que esté graduado. También se presentan en milésimas de pulgada.
El mecanismo consiste en transformar el movimiento lineal de la barra deslizante de contacto, en movimiento circular que describen las agujas del reloj. El reloj comparador tiene que ir incorporado a una galga de verificación o a un soporte con pie magnético que permite colocarlo en la zona de la máquina que se desee. Es un instrumento muy útil para la verificación de diferentes tareas de mecanizado, especialmente la excentricidad de ejes de rotación.
-Rugosímetro: La rugosidad de un material es el conjunto de irregularidades que presenta en su superficie. Realizar de una manera correcta el acabado superficial de una pieza hace que la superficie de esta no tenga ningún tipo de irregularidades y sea completamente lisa.
Para medir la rugosidad de las piezas se utilizan los rugosímetros, que miden la rugosidad media (Rz) y el valor de la rugosidad media (Ra) expresada en micras y muestran la lectura de la medida en una pantalla o documento gráfico.
Limado
El limado tiene como función eliminar parte del material sobrante de una pieza, arrancando virutas o pequeñas partes de la misma para darle un acabado o una forma concretos. Para su realización utilizaremos las limas.
-
Limas: Las limas son barras de acero templado que tienen en su superficie un tallado formado por pequeños dientes, que hacen la función de cuchillas. Las limas suelen llevar también un tallado en su canto y se suelen introducir a presión dentro de un mango que suelen ser de madera o plástico.
Podemos clasificar los diferentes tipos de limas según:
- Su forma
- Su tamaño
- Su picado
- Grado de corte
Clasificación de las limas según su forma
Dependiendo de la superficie a limar utilizaremos una lima u otra, escogiendo siempre la que mejor se adapte a nuestra pieza, a continuación explicare las clases de formas que puede tener una lima y
en qué superficies son las más adecuadas cada una de ellas.
-Planas: Dentro de las planas existen dos variedades, las de punta y las paralelas. Se utilizan en trabajos sobre superficies planas.
-Triangulares: Se utilizan sobre superficies planas y sobre perfiles que formen un ángulo superior a 60º.
-Cuadradas: Se utilizan sobre superficies planas tanto interiores como exteriores y sobre superficies con perfiles a 90º.
-Media caña: Se utilizan para el limado de superficies planas, cóncavas y sobre ángulos menores de 60º.
-Redondas: Se utilizan para el limado de superficies cilíndricas cóncavas.
-De cuchillo: Se utilizan para realizar el acabado de esquinas y en ángulos de 60º.
Clasificación de las limas según su tamaño
Se clasifican según la longitud que tenga el cuerpo de la lima, que suelen venir expresados en pulgadas. Los tamaños mas utilizados son los siguientes:
3", 4", 5", 6", 7", 8", 10", 12", 14", 16" y entre ellos los más utilizados son los de 6", 7" y 8".
Clasificación de las limas según su picado
El picado de una lima expresa el grado de rugosidad que presenta su cuerpo. Puede ser de dos tipos:
-Lima de picado simple: Disponen de unas tallas paralelas (con respecto a uno de los bordes), con una inclinación de 60º a 75º.
-Limas de picado doble: Estas limas disponen de dos tallas, una situada a una inclinación de 40º a 45º con respecto a uno de los bordes, y la otra con una inclinación de 75º a 80º con respecto del borde opuesto, de tal forma que quedan cruzadas transversalmente.
De cara a trabajar con ellas, elegiremos unas u otras dependiendo de la tarea a realizar:
- Las limas con picado doble están especialmente indicadas para trabajar con metales duros.
- Las limas con picado simple desprenden mejor la viruta generada por eso son mejores para trabajar con metales blandos, hay que tener en cuenta también que los metales blandos atascarán rápidamente estas limas.
- Para limar materiales fibrosos, como la madera o plásticos, conviene utilizar unas limas especiales llamadas "escofinas" que presentan unas disposición de dientes alejados e independientes unos de otros.
 |
Lima de picado simple |
 |
lima de picado doble |
 |
Escofina |
Clasificación de las limas según su grado de corte
El grado de corte de una lima depende de el número de dientes que tenga, cuando mayor número de dientes por cm2, más áspera será su superficie, sabiendo esto podemos clasificarlas en:
- Ásperas: 6 dientes/cm2
- Bastas: 8 dientes/cm2
- Semifinas: 12 dientes/cm2
- Finas: 16 dientes/cm2
- Extrafinas: más de 16 dientes/cm2
Como ayuda para su uso podemos seguir estas indicaciones:
- Cuando se ha de arrancar una gran cantidad de material a una pieza ( a partir de 0,5 mm) se comenzará utilizando una lima basta.
- Para alisar una superficie (arranque de material inferior a 0,5 mm) se debe utilizar las semifinas.
- Las limas finas se deben utilizar en las últimas pasadas de acabado para conseguir superficies más lisas (menos de 0,2 mm de material).
Limas especiales
Existen unas limas fresadas que aunque tienen su disposición como limas simples, también realizan el mismo efecto que las limas de efecto doble.
Estas limas se utilizan en carrocería y se llaman garlopas. Se suelen utilizar para el debaste de las reparaciones con estaño, afinado de irregularidades en la chapa, o para marcar irregularidades en la uniformidad de la chapa antes de aplicar el procedimiento de reparación adecuado.
También en el área de carrocería podemos encontrar las llamadas limas de repasar o batir. este tipo de limas se usa para el desbollado y alisado de la chapa, sobre todo en piezas grandes como paños de puerta, laterales de la caja, etc.
 |
Garlopa |
 |
Lima de repasar o batir |
Cuidados y seguridad de las limas
Para la correcta utilización de las limas y para prolongar su duración deberemos realizar los siguientes pasos:
- Trabajar con mangos bien fijados. En caso contrario la espiga puede causar lesiones importantes.
- La lima debe estar perfectamente sujeta sobre el mango para evitar riesgos de accidente.
- Los metales a trabajar deberán ser mas blandos que las limas.
- Durante la operación de limado, parte de las virutas que se desprenden de la pieza se quedan incrustadas en la lima, reduciendo la efectividad de la acción. para limpiar la lima de las virutas incrustadas se cepillan con un cepillo de púas metálicas llamado carda.
- Hay que utilizarlo sobre la lima con cierta periodicidad en el sentido de picado, y en cualquier caso, después de haber sido utilizada. En ningún caso hay que golpear las limas sobre el banco, ya que son muy frágiles y se rompen con facilidad.
- Para evitar la oxidación de las líneas es conveniente aplicarles un barniz protector.
- Para fijar el mango sobre la espiga, hay que deslizarlo sobre la misma y golpearlo contra el banco de trabajo hasta que se agarre perfectamente a la lima.
- Hay que frotar los dientes de la lima con tiza, para evitar que se introduzcan virutas entre los mismos, ya que estas virutas rasparían la pieza al trabajar.
Serrado manual
El serrado es una operación de corte por arranque de viruta que permite quitar de manera rápida el material sobrante de una pieza, mediante unas herramientas llamadas sierras. Con esta operación pueden realizarse trabajos como; ranuras, ingletes, vaciados, etc.
La sierra de mano esta formada por:
Consiste en una lámina flexible o fleje de acero templado al carbono, que presenta una parte lisa, una parte con dientes y unos orificios en sus extremos para su fijación al arco. Cuando una hoja de sierra presenta un dentado en cada lado se denomina entonces "bilateral".
Durante el proceso de corte, los dientes arrancan pequeñas partículas de material que se recogen en los huecos y los conducen fuera del corte. Las hojas bimetales, suelen estar formadas por un cuerpo elástico de acero especial y un listón dentado de acero rápido soldado por rayos de electrones.
Aparte del material de fabricación, las características principales de las hojas de sierra son:
-Las dimensiones de la hoja: Las dimensiones principales son: La longitud, la anchura y el grosor.
- Sierra Unilateral: Longitud - 300 mm, Anchura - 13 mm y Grosor - 0.65 mm.
- Sierra Bilateral: Longitud - 300 mm, Anchura - 25 mm y Grosor - 0.80 mm.
-Paso de dentado: Según la naturaleza del material a cortar, la distancia entre dos dientes consecutivos será más o menos grande, este intervalo se denomina paso del dentado. Si el paso es pequeño, el dentado sera muy fino, en caso contrario será grueso. En la práctica, el paso se expresa en el número de dientes por unidad de longitud (centímetro o pulgada).
En general cuanto más duro o delgado sea el material a cortar, más fino a de ser el paso del dentado que debe tener la hoja correspondiente. En cualquier caso, la correcta elección del tipo de hoja de sierra se debe realizar tomando también en cuenta el material de fabricación de la misma.
-Estructura del dentado: Con el fin de evitar el frotamiento de la hoja contra los bordes del corte practicando en la pieza, y para evitar asimismo el eventual acuñamiento de la hoja, los dientes se tuercen alternativamente a uno y otro lado, consiguiendo que la hoja que la hoja se desplace sin dificultad a lo largo de la hendidura del corte.
El arco
El arco de sierra es el elemento portador de la hoja de sierra. Está formado por un cuadro de hierro plano en forma de "U". Uno de sus extremos está provisto de una empuñadura, y en el otro incorpora un tensor de tornillo o mariposa para mantener la hoja convenientemente tensada.
La hoja se monta sobre el arco introduciendo los orificios laterales en los pasadores o salientes de que disponen tanto la empuñadura como el mecanismo tensor, debiendo quedar suficientemente tensa con el fin de evitar alabeos en el transcurso de la operación de serrado.
Una hoja demasiado floja puede ocasionar los siguientes efectos:
- Un corte imperfecto debido a las desviaciones que originarán las deformaciones.
- Dificultad de deslizamiento de la hoja en la ranura de corte
- Posibilidad de rotura por el excesivo desvío de la sierra respecto a la dirección de corte.
Por el contrario y¡una hoja demasiado tensa puede generar un peligro de rotura al estar sometida a un gran esfuerzo de tracción,
Proceso de serrado
Para realizar un correcto serrado deberemos realizar lo siguiente:
-Siempre que sea posible es recomendable trazar sobre la pieza la línea de corte para poder disponer de una referencia constante en la ejecución del corte.
-Elegir la hoja con el paso adecuado al espesor y tipo de material a cortar, teniendo en cuenta que los materiales blandos, al generar una gran cantidad de virutas, necesitan huecos con capacidad suficiente para alojar y evacuar el material sobrante, por lo que se necesitarán hojas con paso grande.
-Mantener una presión moderada y constante durante todo el movimiento de avance de la sierra, liberando la presión en el recorrido de retroceso. En este último movimiento, es aconsejable bascular ligeramente la sierra con el objeto de facilitar el despegue de los dientes sobre la superficie de la pieza.
-Sujetar adecuadamente la pieza a cortar para evitar cualquier movimiento durante el corte. En caso de utilizar un tornillo de banco, la pieza no debe sobresalir en exceso para evitar vibraciones indeseadas.
-Al iniciar el corte es aconsejable ejercer una presión moderada y con pocos dientes para poder orientar convenientemente la dirección del corte.
-En el movimiento de avance (corte), la hoja debe utilizarse en toda su longitud.
-La rapidez del movimiento de desplazamiento varía entre aproximadamente unos 60 cortes por minuto para materiales blandos y un ritmo aproximado de 30 cortes por minuto para materiales duros.
-El corte debe aproximarse (sin tocar) a la línea de corte previamente trazada, con el fin de permitir una terminación precisa mediante otras operaciones de acabado.
-Los tubos deben girarse a medida que avanza el corte.
-Cuando el material es demasiado duro, deberá disminuirse la velocidad de corte.
-Si la pieza es excesivamente delgada, hay que inclinar ligeramente la hoja en sentido longitudinal para que no se produzcan enganches, hasta conseguir iniciar el corte.
-Cuando se esté finalizando el corte, es aconsejable suavizar la presión ejercida y realizar más lentamente los movimientos.
- Durante la operación es aconsejable refrigerar convenientemente la hoja.
Otras herramientas de serrado
Aparte de la sierra de arco, hay máquinas que funcionan mediante electricidad o por accionamiento neumático. Los más utilizados son:
-Sierra caladora: Es una máquina portátil eléctrica, que permite cortar con precisión varios materiales. Permite hacer todo tipo de cortes: curvos, derechos, biselados.
El corte de la sierra caladora viene dado por el tipo de hoja que se emplee. En general, para cortar metales se utilizan hojas de sierra onduladas con dentado extrafino.
-Sierra circular: La sierra circular sirve para efectuar cortes rectos en chapa fina con gran rapidez. Con ella puede cortarse casi cualquier material con exactitud suficiente si se usa la hoja de corte apropiada. Puede tener un motor eléctrico o ser neumática.
 |
Sierra circular neumática |
-
Sierra de vaivén: Es una herramienta de accionamiento neumático, apropiada para el corte de chapas finas, lo que la hace especialmente indicada para los trabajos de reparación de carrocerías, ya que realizaban un corte preciso, limpio y en cualquier trayectoria.
La palanca lateral de puesta en marcha dispone de un trinquete de seguridad para evitar el accionamiento involuntario.
Sus características de funcionamiento son:
- Velocidad de corte de hasta 10.000 carreras por minuto.
- Presión de aire de 6 a 8 bares.
- Consumo de aire entre 100 y 250 l/min.
- Capacidad de corte de acero de 1.6 mm.
 |
Sierra neumática de vaivén |
Taladrado
El taladrado es una operación de de mecanizado mediante arranque de viruta que tiene por objeto realizar mecanizados en forma de agujeros u orificios de sección circular o cónica, con ayuda de unas herramientas denominadas brocas que se accionan por medio de unas máquinas denominadas taladros. Pueden ser:
-Taladrado de agujero ciego: Un agujero ciego es aquel que se practica en la pieza sólo parcialmente, sin atravesar totalmente.
-Taladrado pasante: Cuando la broca atraviesa por completo a la pieza, realizando un agujero en esta.
-Avellanado: El avellanado es un proceso de mecanizado que consiste en realizar un rebaje de forma cónica en el borde exterior de un agujero. Este rebaje es necesario cuando se utilizan remaches avellanados, y tornillos o pernos de cabeza plana o avellanada. Para realizar esta operación se utiliza una broca para avellanados o una herramienta denominada "Fresa para avellanar".
Brocas
Constituye el elemento principal de la operación de taladrado, y su misión consiste en arrancar el material de la pieza realizando el vacío del agujero. Está constituido por una varilla cilíndrica a la que se la han practicado dos ranuras helicoidales para permitir la salida de viruta, y una vez afiladas en su extremo determinan las aristas cortantes de esta herramienta.
Las superficies que quedan inmediatamente detrás de los filos se encuentran achaflanadas o destalonadas para que únicamente las aristas cortantes entren en contacto con la pieza, evitando así rozamientos indeseados que puedan atascar o sobrecalentar la broca. Con esta disposición la broca adopta la denominación de helicoidal.
Taladradoras
Son las máquinas que generan el movimiento de rotación necesario para realizar los agujeros, en ellas se montan las brocas como herramientas de corte. El movimiento de translación o rectilíneo lo realiza el operario si se trata de una taladradora manual o la propia taladradora cuando dispone de avance automático. Se pueden dividir en:
-Taladradoras portátiles: Pueden ser eléctricas o neumáticas. Las diferencias entre ellas se centran en que las neumáticas son más silenciosas y de menor peso, aunque es necesario disponer de una red de aire comprimido con salidas convenientemente lubricadas. y las eléctricas que son más versátiles y pueden funcionar mediante baterías.
En todas ellas las brocas se sujetan al taladro mediante portabrocas accionados manualmente o a través de una llave especial. Consiste en unas camisas que llevan adosadas tres mordazas con muelles que obligan a estar en contacto con la camisa. La camisa al girar se rosca en un cuerpo y empuja a las mordazas de la broca ciñéndolas sobre esta, realizándose así la fijación.
Este tipo de taladros tienen una reducida gama de revoluciones por lo que resultan poco operativas para determinados trabajos, aunque la gran ventaja que ofrecen es que proporcionan una gran accesibilidad a cualquier zona para realizar el taladrado.
Algunos tipos son:
- Taladradoras angulares (ángulo recto): son muy utilizadas para poder operar en lugares de difícil acceso.
- Minitaladradoras: Son unas pequeñas taladradoras que alcanzan un gran número de revoluciones, lo que le hace especialmente indicado para brocas de tamaño pequeño.
- Percutoras: En este tipo de máquinas, además del movimiento circular, la broca tiene otro movimiento axial alternativo para poder taladrar materiales como el cemento.
-Taladradoras fijas: proporcionan una mayor comodidad y precisión en los trabajos de taladrado. Van equipados con un portabrocas similar al de los portátiles, una base donde se sitúa un conjunto de mordazas móvil y orientable, una manivela o palanca para dar avance a la broca y un sistema de poleas para modificar la velocidad de la broca. A su vez pueden dividirse en:
- Sensitivas (de accionamiento manual), generalmente de sobremesa
- De columna (manuales o automáticas), que apoyan directamente contra el suelo.
Los taladros de columna son mayores que los de sobremesa, por lo que se pueden realizar taladros en piezas más grandes. Habitualmente disponen de una mesa giratoria tanto en el plano vertical como en horizontal. Pueden trabajar con brocas de mayor diámetro. En algunas ocasiones puede ser necesario interponer un casquillo reductor morse entre la broca y el husillo. Las taladradoras de columna pueden ofrecer un elevado número de prestaciones , como: girar en ambos sentidos, disponer de un circuito de refrigeración para las piezas a taladrar, incorporar un sistema de iluminación propio junto al portabrocas, programarse para que avancen automáticamente en función de unos parámetros.
 |
Taladradora de sobremesa |
 |
Taladradora de columna |
Proceso de taladrado
El proceso para realizar correctamente la operación de taladrado se puede ver a continuación:
-Agarrar la broca mediante el portabrocas de la máquina taladradora o introduciendo a presión el cono morse.
-Sujetar correctamente la pieza a taladrar sobre la mordaza, utilizando para su defecto amarre bridas, calzas, etc. Esta operación es sumamente importante para evitar que las piezas puedan ser arrastradas por las brocas.
-Realizar un graneteado del centro del agujero para guiar a la broca.
-Antes de realizar agujeros de diámetro elevado, conviene pretaladrar previamente la pieza con una broca de diámetro inferior. Antes de poner en marcha la taladradora hay que vigilar que la punta de la broca no esté en contacto con la pieza.
-Seleccionar adecuadamente la velocidad de giro y el avance adecuado en función del tipo de broca, diámetro y naturaleza del material a trabajar. La selección de la velocidad adecuada puede realizarse mediante poleas, engranajes o electrónicamente.
-Durante la operación de taladrado, la forma de la viruta generada vendrád eterminada por el tipo de material a trabajar, por el tipo de broca utilizada, la velocidad de corte y por el avance aplicado. Normalmente, los materiales blandos suelen producir virutas largas. Conviene sacar la broca cuando la viruta no salga al exterior.
-Refrigerar adecuadamente la zona de contacto entre broca y pieza para poder reducir el rozamiento y mantener una temperatura baja en la broca.
Normas de seguridad e higiene en el taladrado
- No acercar la cabeza al portabrocas, puesto que podría engancharse en el pelo.
- No tocar las virutas generadas, ya que son altamente cortantes.
- No acercar demasiado la mano a la zona de contacto con la pieza.
- Extremar las precauciones al sujetar la pieza para evitar que se enganche al movimiento del portabrocas o que salga despedida a gran velocidad.
- Extremar las precauciones si se sopla con aire comprimido para limpiar las virutas.
- Utilizar las prendas de protección personal adecuadas: gafas o careta de protección facial y peto de cuero.
- No tocar la broca estando aún caliente.
- No sujetar con las manos una pieza en movimiento.
Roscado
Con el Término rosca se designa una configuración de trayectoria helicoidal, elaborada por un cuerpo de revolución, generalmente cilíndrico. También puede considerarse a una rosca como el arrollamiento en forma de hélice de un perfil sobre un cilindro. Dependiendo de que la ejecución de la rosca sea en la parte interior o exterior de la superficie de la pieza determinada, se obtienen roscas interiores o exteriores respectivamente.
Básicamente, las aplicaciones más importantes en las roscas son:
- Como elementos de fijación o sujeción en uniones amovibles con lo que se consigue todo tipo de uniones y ensamblajes.
- Como sistemas transformadores de movimiento.
Terraja (cojinete)
Básicamente, roscar un tornillo consiste en eliminar, de un trozo de material cilíndrico, de diámetro ligeramente menor al exterior de la rosca, la parte del material sobrante entre filete y filete, es decir, practicar una acanaladura helicoidal sobre dicho cilindro . Para la realización del roscado sobre varillas cilíndricas, estas han de presentar una superficie perfectamente lisa y regular, empleándose una herramienta de corte denominada terraja o cojinete.
La terraja consiste en una especie de tuerca fabricada con aceros de alta calidad, que disponen de unas ranuras longitudinales de sección circular, que conforman las aristas de corte y determinan las caras de desprendimiento, facilitando la salida de material cortado. Una de sus dos caras lleva la entrada, que consiste en un avellanado que facilita el centrado e inicio de la rosca en la varilla o perno.
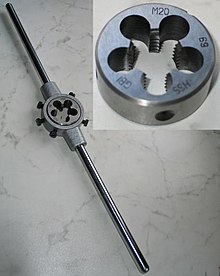 |
terraja y portaterrajas |
-
Proceso de roscado manual de un tornillo:
- Inmovilizar la varilla sobre un tornillo de banco o cualquier otra herramienta de sujeción adecuada.
- Introducir la terraja en el portaterrajas, con el lado de inicio de la rosca hacia fuera, y colocada de tal manera que el lado de cierre del portaterrajas empuje la terraja contra la varilla a roscar, ya que en caso contrario serían los tornillos de inmovilización los que soportarían el esfuerzo de empuje.
- Iniciar el roscado situando la terraja perpendicularmente a la varilla y girando el portaterrajas en ciclos de media vuelta en sentido de avance y 1/4 de vuelta hacia atrás, para cortar y eliminar la viruta desprendida.
- Debido al rozamiento producido por el proceso de corte, es necesario lubricar constantemente la zona roscada con aceite de corte o "taladrina".
Macho de roscar
Para realizar roscas sobre taladros, las herramientas empleadas son unos "tornillos" de acero al carbono y templados para darles mayor dureza, a los cuales se les han practicado tres o cuatro ranuras longitudinales que conforman las aristas de corte. La configuración de estas determina las caras de desprendimiento que permiten la salida del material cortado o viruta. La cara de incidencia se genera mediante un destalonado realizado en la entrada del macho. Se presentan, generalmente, en juegos de tres para facilitar el tallado progresivo de la rosca.
-Proceso de roscado manual de un taladro:
- Sujetar adecuadamente la pieza a roscar, normalmente en un tornillo de banco.
- En primer lugar se ha de introducir el macho de roscar número uno de "prerroscado", utilizando el portaherramientas denominado "giramachos" o "bandeador", comprobando que en todo momento su posición es completamente perpendicular a la pieza a roscar, por lo que resulta aconsejable utilizar una escuadra para evitar inclinaciones. Con los machos actuales se recomienda roscar de una manera continua, sin realizar movimientos de retroceso que produzcan un desafilado de la herramienta
- A continuación, se pasará el segundo macho de roscar. Este tiene el extremo menos cónico y los filetes de la rosca algo más perfilados.
- Por último, se introducirá el tercer macho de la serie. Se denomina de acabado y prácticamente no presenta forma cónica ninguna, estando los filetes de la rosca con un perfil totalmente definido.
Y hasta aquí la entrada de hoy, más extensa de lo normal, pero considero que más completa de lo que os tengo acostumbrados,indicio de que solo se puede ir a mejor amigos!!
Un saludo y hasta la próxima ;)